Reducing Telecom Truck Roll Operation Costs with Automation
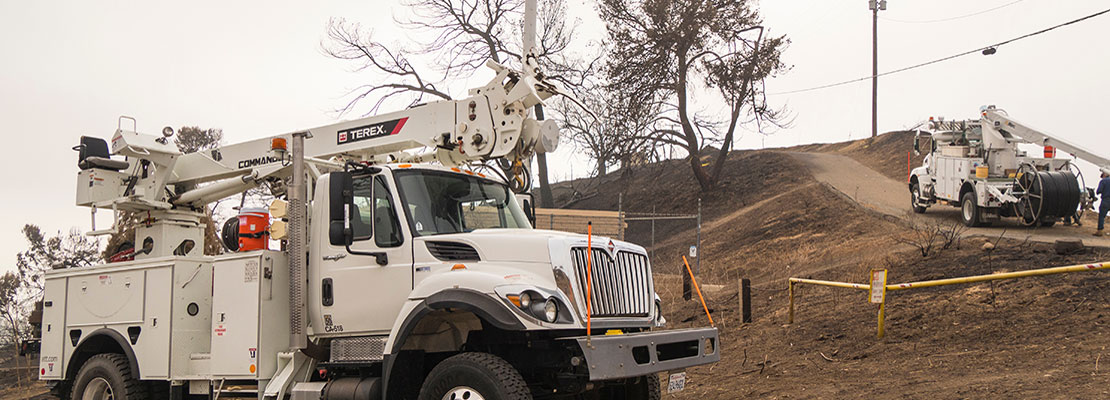
In a very competitive global industry, telecom operators must balance the ongoing customer satisfaction against reducing company operating costs. One of the most significant costs in managing telecom towers are site visits or truck rolls. Truck rolls refer to situations where a site engineer or field service technician is dispatched, usually involving a vehicle, to perform some form of technical service.
Challenges with Truck Rolls in the Telecom Industry
In the telecom industry, the need to dispatch a technician to a location for troubleshooting is a large expense for operational departments. These site visits include the technician’s time for travel and the service visit, as well as the raw cost of transportation (mileage). There are also several telecom organizations that have greenhouse gas (GHG) initiatives; so by reducing the amount of drive time saves both money and reduces emissions. Truck rolls also contribute to potential accidents, as any extra drive time has the risk for potential accidents. These accidents are also more likely to occur during off-hours, which is a common scenario in the case of cell site outages.
For many telecom operator’s current environments, only the most basic alarms (a “power” alarm) will be known to indicate what is going wrong at a site. This results with a first truck roll being done to simply troubleshoot what is going on at a site. Maybe a single visit will be sufficient to clear the alarm, but in other cases the first visit might only be to discover that an additional visit will be necessary to solve the core problem. In other cases, a visit may be made turn out to be for no reason, or something that could easily have waited for a more routine visit to fix.
Why are Truck Rolls Causing Problems for Telecom Operators
There are some truck rolls that cannot be avoided, and dispatching a technician on-site should really be considered a last resort after a careful review to confirm its validity and necessity. Here are a few examples of truck rolls that can be avoided:
- Situations where the on-site issues can be easily resolved, as nothing apparent is wrong once the site visit is made. Although difficult to determine, such no fault found (NFF) dispatches are estimated to account for 17%-20% of visits made by telecom operators.
- According to an Aberdeen Group report, 25% of all service calls require at least one additional visit to solve customer needs. The reasons are various: dispatching an unqualified technician, the absence of the right part or tools, or failure to account for special conditions in the service area like the lack of site access.
To reduce these unnecessary truck roll costs and inefficiencies, telecom operators must find better solutions for better managing truck rolls, as well as for resolving more issues remotely.
How Do Telecom Operators Measure the Cost of Truck Rolls
According to OSP magazine, the telecom industry analysts estimate the cost of the average truck roll at anywhere from $150 to $600, depending on the location, the work being done at the site, and the technician’s skill level and salary. This estimate can increase if the truck roll is at night and the technician is being paid overtime. In fact, the Technology Service Industry Association reports that the real cost of a typical truck roll is upwards of $1,000 each time. A truck roll expense is determined by these three main factors:
- Labor Cost – this is the largest component of truck roll costs and it includes transportation preparation, transition costs and non billable service time, and overtime. Additionally, there are Union contracts which may specify a minimum number of hours that on-call technicians are paid for every truck roll, regardless of how long the site visit actually takes.
- Truck/Transportation Cost – this includes the cost of maintenance, gas usage and rental/ownership costs, including insurance and depreciation costs. In practice, it simply means that the more often the trucks are used, the faster the vehicle assets will depreciate, and therefore the need to conduct more maintenance on vehicles to keep them in commission becomes unavoidable.
- Competitive Issues/MTTR – For mobile network operators, a major cost often relates to the reputation of the network. In selling to business customers, for example, the deciding factor on which network to use might relate to which network is considered the most reliable. One element of which is how long a site remains down after a fault. This relates to a basic network metric of mean time to repair, or MTTR. For other types of telecom networks, MTTR may be valued even more highly. This is a critical factor to consider for public safety networks, especially when lives may be at stake when a network is down.
How Can Telecom Operators Optimize Truck Rolls
Truck rolls represent a costly challenge for the telecom industry and the best option to optimize truck rolls is to implement a telecom site automation solution. A telecom automation solution can increase visibility into what might be causing a site to not properly function, and could even allow for a site problem to be resolved directly from the network operation center (NOC). Telecom site automation systems can reduce truck rolls in three primary ways.
- Improved Visibility – A telecom site automation appliance can be interfaced to all underlying power, security, and environmental subsystems. Commonly the data from a telecom site automation appliance will provide potentially hundreds of variables back to business intelligence software dashboards, which can easily display the inter-relation between many different systems at once.
- Remote Access – By utilizing a telecom site automation appliance, it can become a single place to pass through to underlying “smart controllers”. In many cases, smart controllers are not currently connected to anything at a site. There is also the variety of different makes and ages of these controllers makes managing them difficult – unless you have a site automation appliance that can connect them all.
- DC Reboot – You have the ability to even directly reboot equipment with a telecom site automation appliance. This can be done directly from the NOC, or can even be done autonomously by the site device itself. Examples include the site appliance receiving an alarm from a piece of equipment and attempting to clear the alarm on its own by rebooting a piece of equipment and checking again for the same alarm, or even turning off the entire site as various stages of power loss occur.
When on-site service truck rolls are avoided, service costs are decreased, and customer satisfaction increases as problems are resolved more quickly. The technicians will also have more time to work on direct revenue producing site upgrades and other higher priority activities.
Modernize Your Service Organization and Reduce Your Truck Rolls
Automation is improving processes within most industries around the world. Learn what some of the leading network operators are doing with telecom site automation to improve their network and service operations. Feel free to contact us to learn more!